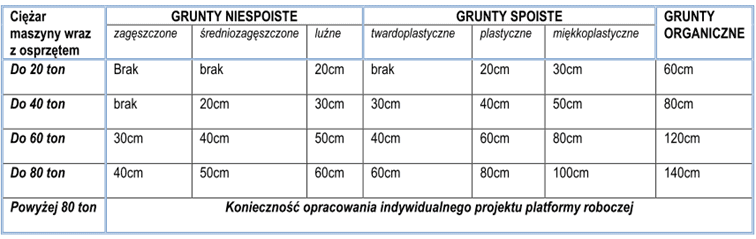
Dodatkowo wypunktowano następujące wymagania ogólne:
- Materiał: przekrusz betonowy lub ceglany, kruszywo łamane lub pospółka.
- Zaleca się dogęszczenie gruntów niespoistych, średnio zagęszczonych i luźnych.
- Powierzchnia platformy poszerzona w stosunku do zakresu wykonywania prac – wymiary maszyny.
- W przypadku pracy na terenie podmokłym należy przewidzieć wykonanie rowu odwadniającego.
- Drogi dojazdowe do platformy min. 6,0m.
- Zjazd na platformę roboczą o szerokości min. 6,0m, maksymalne nachylenie 1:4.
- W przypadku gruntów słabych zastosowanie geosyntetyków separacyjnych.
- W przypadku pracy w pobliżu skarp nasypów/wykopów należy zweryfikować stateczność globalną budowli ziemnej szczególnie, gdy pracują tam maszyny robocze ciężkie.
W przypadku bardziej skomplikowanych warunków takich jak bardzo ciężki sprzęt, bardzo słabe podłoże gruntowe, platformy robocze usytuowane w wykopach, na skarpach, nasypach lub na zróżnicowanych poziomach, należy każdorazowo stosować indywidualne podejście. Przygotowanie placu budowy do prowadzenia robót zasadniczych musi być przedmiotem analizy inżynierów kilku branż, przedstawicieli generalnego wykonawcy i wykonawców specjalistycznych. Fakt zrozumienia istotności problemu związanego z platformami roboczymi przez największe firmy budowlane w kraju jest dużym krokiem w kierunku podniesienia poziomu bezpieczeństwa na budowach. Coraz częściej jakość platform roboczych staje się przedmiotem analizy firm ubezpieczeniowych, które wielokrotnie uczestniczą w pokrywaniu strat materialnych wynikających z uszkodzeń mienia i sprzętu pracującego na placu budowy. Jako wypadki powodujące największe straty materialne można wskazać utratę stateczności maszyn takich jak palownice używane do wykonania pali fundamentowych czy kolumn przemieszczeniowych.